LIFTING EQUIPMENT AND ACCESSORIES (LOLER)
ERD Engineering Inspections Ltd carry out the inspection/thorough examination of lifting equipment and lifting accessories covered by the Lifting Operations and Lifting Equipment Regulations 1998 (LOLER).
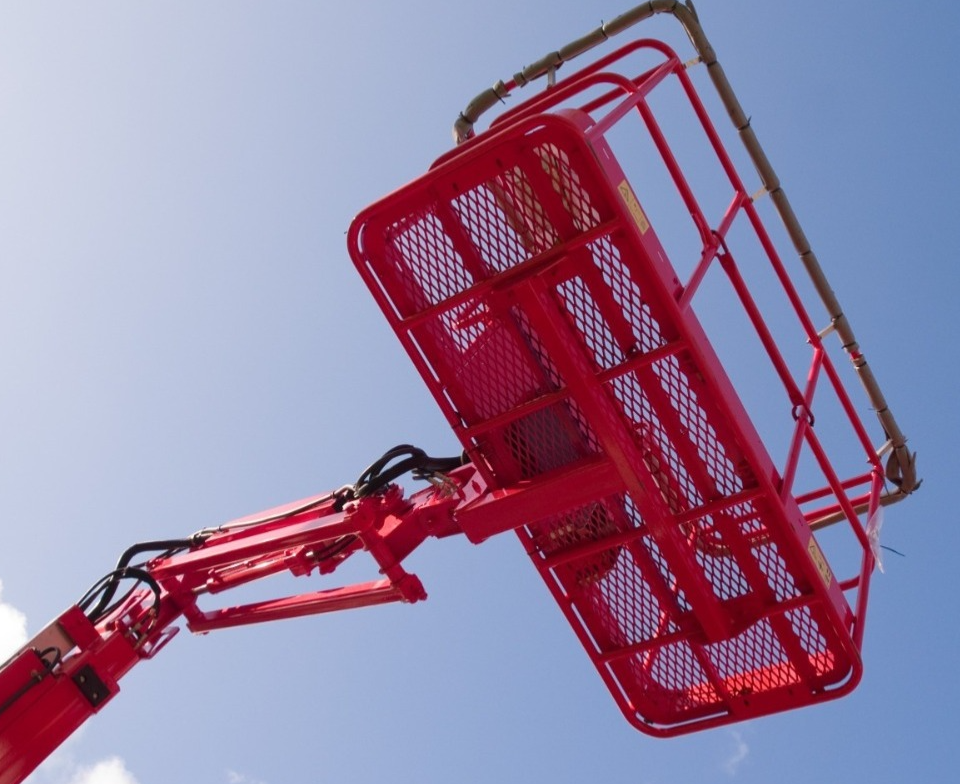
WHAT IS LOLER?
LOLER stands for Lifting Operations and Lifting Equipment Regulations 1998. The regulations place legal duties on people and companies who own, operate or have control over lifting equipment. This includes any business or organisations whose employees use lifting equipment, whether the equipment is owned by them or not.
Lifting Operations - an operation concerned with the lifting or lowering of a load. A 'load' is the item or items being lifted, which includes a person or people.
Lifting Equipment - work equipment for lifting and lowering loads. This includes lifting accessories and attachments use for anchoring, fixing or supporting the equipment.
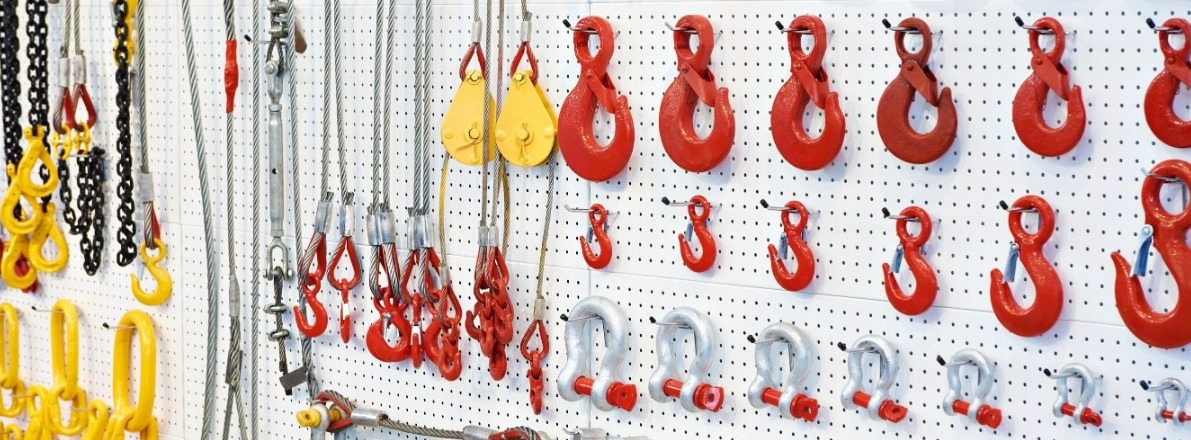
WHAT DO I NEED TO DO?
LOLER requires that all equipment used for lifting is fit for purpose, appropriate for the task, suitably marked and is subject to a Thorough Examination.
It is the duty holders responsibility to ensure that an independent and impartial LOLER inspection can be carried out at statutory intervals. You should ensure that the person carrying out a thorough examination is a competent person and has such appropriate practical and theoretical knowledge and experience of the lifting equipment to be thoroughly examined as will enable them to detect defects or weaknesses and to assess their importance in relation to the safety and continued use of the lifting equipment.
The Lifting Operations and Equipment Regulations 1998 state that the competent person carrying out LOLER inspections must be "sufficiently independent and impartial to allow objective decisions to be made" This means that they are not the same person responsible for the servicing and maintenance, as they would be checking their own work and thorough examinations should be made without fear or favour.
In addition to a thorough examination under LOLER, the person responsible for the lifting equipment (the owner or operator) must carry out reasonable and regular checks before use.
WHAT IS A THOUROUGH EXAMINATION?
The aim of the thorough examination is to confirm the equipment is safe to use until the next examination and will help to identify any issues before they become serious.
The competent person will carry out a systematic and detailed examination of the equipment and safety critical parts. These checks may include visual examination and functional checks, measurements of wear and in some cases non-destructive testing and load testing. Some disassembly or internal examination of parts may also be required.
The inspecting engineer will provide a report of thorough examination. The report will confirm whether the equipment is safe to use until the next examination or if any defects are identified. If defects are identified they should be reported to the person responsible for the equipment as well as the relevant enforcing authority (HSE for industrial workplaces and Local Authorities for most other workplaces).
This report must contain the information required by regulations, including:
- the examination date
- the date when the next thorough inspection is due
- any defects found with are, or could potentially become, a danger to people
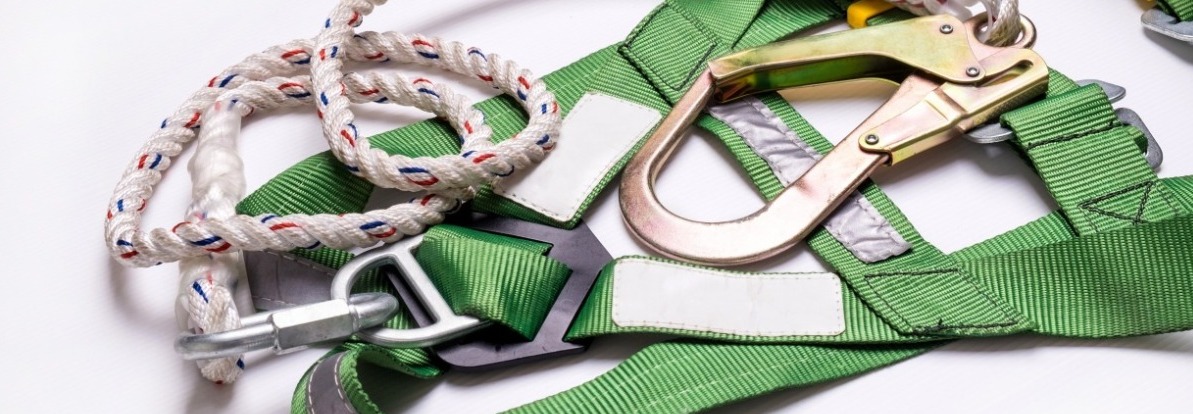
HOW OFTEN SHOULD MY LIFTING EQUIPMENT BE INSPECTED?
In order to verify that lifting equipment and accessories remain safe for use and to detect any deterioration in good time, thorough examinations are required throughout the lifetime of the equipment.
A thorough examination should be carried out :
- before first use, unless there is a valid Declaration of Conformity that is less than 12 months old and was not assembled on site
- after on site assembly and before each use on site - where it depends on installation, or re-installation / assembly at another site before use, e.g. tower cranes
- regularly while in service - Most lifting equipment will be subject to wear and tear and so will need regular in-service examination
- where it is exposed to conditions causing deterioration, liable to result in dangerous situations e.g. environmental conditions
- after exceptional circumstances that may have caused damage and effect the safety of the lifting equipment
- following changes to the equipment such as modifications or repair of critical parts
- 6 months, for lifting equipment and accessories used to lift people as well as protective equipment such as harnesses and lanyards
- 6 months, for all lifting accessories, any equipment used to attach loads, such as slings, chains, shackles etc
- 12 months, for all other lifting equipment such as cranes, forklift trucks, vehicle lifts, access platforms etc.
The competent person carrying out the examination may ask for inspections to be carried out more frequently depending on the condition of the item and the operating conditions.